Labor and Human Rights
We believe companies play a vital role in implementing and respecting labor and human rights. Our programs aim to ensure all our people are treated with respect and dignity, not only within our own operations, but throughout our supply chain (see Responsible Supply Chain). I 103-1 I
The main management systems and programs we use to monitor, control, and improve labor conditions in our operations are:
- A Corporate Labor and Human Rights policy deployed throughout our operations (available at www.st.com).
- An internal audit program on labor and human rights, targeting our manufacturing sites.
- Responsible Business Alliance (RBA) human rights self-assessments at all major ST sites, and third-party RBA audits at our 11 largest manufacturing sites.
- Multiple initiatives to uphold human rights and mitigate risks in regions we operate in (see Advancing labor and human rights, below).
Integrating human rights into our business
As a member of the RBA since 2005 (and currently a full member), we enforce the most advanced standards and have a comprehensive due diligence process that covers nine core principles.
Our due diligence approach
We apply a due diligence process based on RBA methodology to continually improve our management systems and prevent and mitigate human rights abuses from occurring.
Commitment
We are committed to the RBA code of conduct and integrate its principles into our internal policies:
We deploy regular labor and human rights training at our manufacturing sites.
- More than 35 employees have attended RBA in-person training to be able to deploy the RBA code of conduct and Validated Assessment Program (VAP) audit standard.
- In 2021, we trained 72% of our manufacturing employees on the RBA code of conduct, particularly on labor and human rights issues relevant for the local context.
Communication
We communicate how we are addressing our risks and impacts.
- Our performance is reported publicly every year in our annual Sustainability report.
Risk assessment
We conduct regular risk assessments to identify and evaluate actual or potential adverse human rights impacts.
Our risk assessment is based on:
- An assessment of our inherent risks related to our activities and locations.
- RBA self-assessment questionnaires, which our sites complete each year. In 2021, our sites scored from 90/100 to 95/100, which is higher than the industry average of 89/100.
- A site-specific assessment to identify the labor and human rights risks associated with local operations of our major sites.
Audit programs
We run audit programs covering our manufacturing sites (>80% of our employees).
- Our internal audits monitor compliance with our Labor and Human Rights policy (covering our nine core principles). They are conducted across all our manufacturing sites at least every three years.
- RBA third-party audits are conducted at our 11 largest manufacturing sites every two years, including closure audits when relevant.
Improvement actions
We identify and implement appropriate actions to prevent and mitigate adverse human rights impacts.
- Following the risk assessment, we develop and implement mitigation actions to prevent or minimize any labor and human rights impacts identified.
- Our internal and external audit results are followed up at both site and corporate level. Where appropriate, we implement corrective action plans to resolve any issues identified, and we verify that the actions have been completed.
Performance monitoring and review
We track and measure our progress to continuously improve our performance.
- Site performance is regularly monitored and reviewed through specific objectives and targets.
- Our action plans are tracked to measure and improve their effectiveness in addressing the impact of adverse human rights.
Commitment
We are committed to the RBA code of conduct and integrate its principles into our internal policies:
We deploy regular labor and human rights training at our manufacturing sites.
- More than 35 employees have attended RBA in-person training to be able to deploy the RBA code of conduct and Validated Assessment Program (VAP) audit standard.
- In 2021, we trained 72% of our manufacturing employees on the RBA code of conduct, particularly on labor and human rights issues relevant for the local context.
Communication
We communicate how we are addressing our risks and impacts.
- Our performance is reported publicly every year in our annual Sustainability report.
Risk assessment
We conduct regular risk assessments to identify and evaluate actual or potential adverse human rights impacts.
Our risk assessment is based on:
- An assessment of our inherent risks related to our activities and locations.
- RBA self-assessment questionnaires, which our sites complete each year. In 2021, our sites scored from 90/100 to 95/100, which is higher than the industry average of 89/100.
- A site-specific assessment to identify the labor and human rights risks associated with local operations of our major sites.
Audit programs
We run audit programs covering our manufacturing sites (>80% of our employees).
- Our internal audits monitor compliance with our Labor and Human Rights policy (covering our nine core principles). They are conducted across all our manufacturing sites at least every three years.
- RBA third-party audits are conducted at our 11 largest manufacturing sites every two years, including closure audits when relevant.
Improvement actions
We identify and implement appropriate actions to prevent and mitigate adverse human rights impacts.
- Following the risk assessment, we develop and implement mitigation actions to prevent or minimize any labor and human rights impacts identified.
- Our internal and external audit results are followed up at both site and corporate level. Where appropriate, we implement corrective action plans to resolve any issues identified, and we verify that the actions have been completed.
Performance monitoring and review
We track and measure our progress to continuously improve our performance.
- Site performance is regularly monitored and reviewed through specific objectives and targets.
- Our action plans are tracked to measure and improve their effectiveness in addressing the impact of adverse human rights.
Our risks and improvement actions
In 2021, the main risks we identified and the preventive and corrective actions we implemented are described in the table below.
Description |
Actions implemented |
---|---|
Control and monitoring of working hours (including rest days) |
|
Prevention of forced and bonded labor |
|
Supplier responsibility |
|
|
|
Student protection and management |
|
Our audit programs
Internal audit
for manufacturing sites
We run internal audits on labor and human rights and third-party RBA Validated Assessment Program (VAP) audits at our manufacturing sites. These audits highlight any gaps at the sites, help to identify areas that require improvement, and strengthen the local social responsibility culture.
In 2021, we conducted six labor and human rights internal audits, all of them remotely.
Regarding RBA VAP (6.0/7.0) third-party audits, our 11 largest manufacturing sites have been audited this year, either in an initial audit or in a closure audit, or both.
- Our best performer with full compliance during the initial audit was our Catania site (Italy).
- Initial audit results at our Crolles, Rousset and Tours sites (France), and our Bouskoura site (Morocco), were well above the industry average of 134/200.
- For closure audits, our Agrate (Italy), Ang Mo Kio (Singapore), Calamba (the Philippines) and Muar (Malaysia) sites were fully compliant, with a score of 200/200.
- Our Kirkop site (Malta) resolved 100% of the 38 non-conformances identified during the initial audit in January 2021.
- Our Shenzhen site (China) received RBA silver recognition.
Our average RBA audit score is above the industry average: +10 points in initial audits and +20 points in closure audits. I 103-3 I
Country |
Site |
SAQ score |
VAP score |
||||||
---|---|---|---|---|---|---|---|---|---|
High risk |
|||||||||
China |
Shenzhen |
94.4 |
187.1 |
||||||
Malaysia |
Muar |
94.6 |
200 |
||||||
Singapore |
Ang Mo Kio |
92.1 |
200 |
||||||
The Philippines |
Calamba |
90.7 |
200 |
||||||
Medium risk |
|||||||||
Malta |
Kirkop |
91.4 |
200 |
||||||
Morocco |
Bouskoura |
94.3 |
173.5 |
||||||
Low risk |
|||||||||
France |
Crolles |
92.3 |
177.4 |
||||||
Rousset |
92.7 |
190.1 |
|||||||
Tours |
93.1 |
187.1 |
|||||||
Italy |
Agrate |
91.9 |
200 |
||||||
Catania |
94.1 |
200 |
|||||||
|
The main non-conformances identified during third-party RBA audits in 2021 are described in the table below.
Number of audits: 12 |
|
|
|
||
Total of major non-conformances |
|||||
Labor, Ethics |
Management systems |
||||
---|---|---|---|---|---|
Working hours |
6 |
Supplier responsibility |
2 |
||
Wages and benefits |
2 |
Training |
2 |
||
Freely chosen employment |
3 |
Audits and assessments |
1 |
||
Non-discrimination |
2 |
Improvement objectives |
1 |
||
Young workers |
2 |
Company commitment |
2 |
||
Intellectual property |
1 |
Management accountability and responsibility |
2 |
||
No improper advantage |
1 |
Legal and customer requirements |
1 |
||
Environment, Health and Safety |
|||||
Emergency preparedness |
5 |
Occupational safety |
2 |
||
Occupational injury and illness |
1 |
Health and safety communication |
1 |
||
|
Following internal and external audits, we have implemented improvement plans to reinforce existing social management systems.
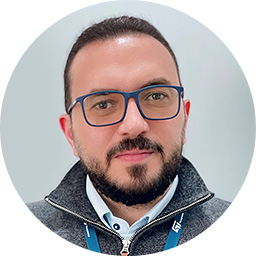
Mahmoud Okasha
Sustainability Champion, Kirkop (Malta)
The RBA audit program is challenging. It requires us to continuously build capability on the RBA standard, which is revised every three years. Following the results of our site’s initial RBA audit, we worked on rapidly implementing appropriate actions to address non-conformances, including a deep analysis of root causes. This has helped us improve the effectiveness of our management system and enhance our social performance."
FOCUS
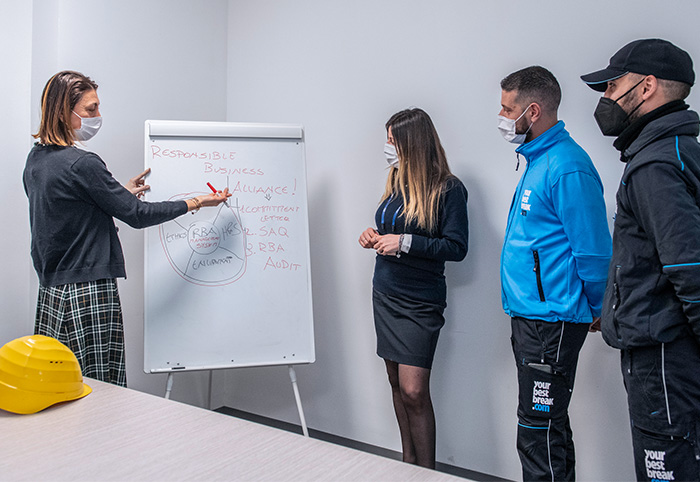
Managing our improvement action plans
Corrective Action Plan (CAP) management is an important part of our management systems to mitigate any risk or correct any non-conformance.
For both internal and external audits, our CAPs are defined at site level with the relevant stakeholders, then they are reviewed and challenged at corporate level to improve our management systems, share best practices, reduce risks, and identify opportunities.
For both internal and external audits, our CAPs include:
- determination of root cause(s)
- description of the preventive and corrective actions to address the root cause(s) identified and prevent future recurrence of the issue(s)
- the date by which the actions are expected to be completed
These CAPs are defined, implemented, and reviewed following defined timelines, and we verify that the findings are closed.
Advancing labor and human rights
Since its launch in March 2020, our STCare employee assistance program has been improved to strengthen our efforts to protect and support our employees during the pandemic and beyond (see Health and Safety).
We implemented many initiatives to support our most vulnerable employees, such as a salary increase in all countries in November 2021. Some of our sites, including Calamba (the Philippines) and Muar (Malaysia), also supported the local vaccination campaign through on-site vaccination programs (see Health and Safety).
Contributing to the Sustainable Development Goals
Our commitments and programs as described above contribute to:
SDG target 8.7 – Take immediate and effective measures to eradicate forced labor, end modern slavery and human trafficking, and secure the prohibition and elimination of the worst forms of child labor.
SDG target 8.8 – Protect labor rights and promote safe and secure working environments for all workers.
SDG target 17.16 – Enhance the global partnership for sustainable development, complemented by multi-stakeholder partnerships that mobilize and share knowledge, expertise, technology and financial resources, to support the achievement of the sustainable development goals in all countries, in particular developing countries.
2025 sustainability goal |
Status |
Comments |
||
SG5: Get 100% of ST manufacturing sites recognized for social responsibility by external international bodies by 2025. |
73% of largest manufacturing sites – 8/11 RBA platinum recognition or a score of 200/200* |
|||
|
Annual sustainability goal |
Status |
Comments |
100% of priority, major and minor non-conformities closed during the RBA closure audit. |
96% of findings closed (48/50) |
|
100% of all manufacturing sites audited every 2 years for compliance with the RBA standard. |
100% of largest manufacturing sites audited (11/11) |