Responsible Supply Chain
A responsible supply chain is essential to sustainable business success. At ST we are committed to partnering with suppliers who share our values of respecting people and driving business with integrity and excellence, and we expect the highest standards from them.
Our supply chain
What we buy and where we buy it from
44%
of procurement spend in Europe
We procure materials, goods, and services from approximately 6,500 tier 1 suppliers of various types and sizes. Our suppliers range from external manufacturing subcontractors, material suppliers, equipment and spare-parts suppliers, to onsite service providers and labor agencies. In 2021, around 49% of our procurement spend was with suppliers based in Asia and 44% in Europe. 37% of our procurement volume is managed locally. The rest is managed centrally at corporate level. I 204-1 I
Starting in 2021, we have aligned our suppliers’ categories with the Responsible Business Alliance (RBA) definitions. Direct suppliers are those who provide services or materials for finished goods. Our equipment and spare-parts suppliers are now categorized as indirect suppliers, which represent half of our procurement volume.
Procurement volume by category | 102-9 |
Evolving legislation
Due diligence
committee
We keep up to date with the numerous regulations that have been published regarding due diligence in the supply chain. All our tier 1 suppliers are screened automatically and continually against restricted party lists. We organize a due diligence committee twice a year involving different corporate organizations to discuss our supply chain sustainability management. At the end of 2021, we created an additional transversal task force that meets twice a month, which aims to adapt our supply chain management approach to reflect forthcoming legislation on forced labor.
Risk management
Business risks
In the current challenging conditions of the global economy, we identify strategic suppliers (critical for the business) according to the spend level, the scarcity of their product, and the availability of alternative sources. These strategic suppliers are periodically assessed, providing the flexibility our global procurement organization needs to secure business continuity.
We implemented a new supply chain risk management tool in our procurement team in 2021. Harnessing big data, machine learning and artificial intelligence technology, this real-time supplier information platform informs our buyers about any new threats or events potentially impacting our supply chain, triggering proactive action or recovery plans whenever necessary to prevent or mitigate the risk.
Sustainability risks
We perform an annual risk assessment of our tier 1 suppliers that enables us to identify, manage, mitigate, or avoid sustainability risks within our supply chain, if possible.
Annual
risk assessment
Our 2021 risk assessment was based on the results of a supply chain intelligence platform, using publicly available as well as audit data. We weighted this with specific semiconductor sector metrics, including the location of supplier facilities. This process allowed us to identify 810 suppliers with a score above 4.8 out of 10. We then fine-tuned the process for service providers, according to spend, regular presence of suppliers on site, and activities at risk. Ultimately, 376 suppliers across 616 facilities were identified as being at risk in terms of sustainability.
Monitoring
In our standard contract, suppliers declare that they have read and understood ST’s Business Ethics and Corporate Responsibility Statement and that they acknowledge and agree to comply with the latest version of the RBA code of conduct. This established standard ensures that working conditions are safe, workers are treated with respect and dignity, and business operations are ethically and environmentally responsible. By agreeing to comply with the RBA code, suppliers are also required to deploy the code to their own supply chain.
In addition to this, our suppliers at risk follow a rigorous process based on the RBA methodology, adopted in 2005 and deployed progressively in our supply chain since then. It comprises three main steps.
In 2021:
- 90% of our suppliers at risk signed the RBA commitment letter.
- 434 suppliers’ facilities completed a SAQ.
- 38 facilities of direct suppliers (subcontractors, material suppliers) and 5 equipment and spare part suppliers’ facilities had a third-party RBA audit.
- 36 local, indirect service providers (canteen, cleaning, security, gardening, dormitories, maintenance, labor agencies, etc.) had a second-party audit.
All audited suppliers with non-conformances are obliged to put corrective actions in place. These are verified in a follow-up closing audit.
If the supplier is unable or unwilling to meet these requirements, sanctions may be taken. Possible actions include:
- sending a warning letter from executive management
- selecting alternative products or services to decrease the supplier’s market share
- temporary or definitive termination of the contract and the supplier being blacklisted
Top 5 audit findings of material, equipment/spare-parts suppliers and subcontractors(1) | 308-2 | 414-2 |
Top 5 audit findings of local service providers(1) | 308-2 | 414-2 |
FOCUS
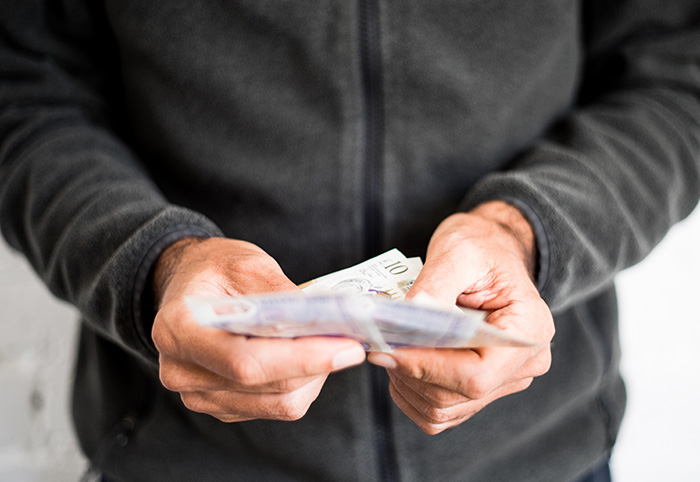
Recruitment fees remediation: from policy to practice
As an RBA member, ST is publicly committed to eradicating recruitment fees from its supply chain to protect vulnerable groups, including migrant workers. Direct communication with our suppliers, SAQs and audits allow us to detect if workers have paid recruitment fees or other related fees.
In such cases, we adopt an inclusive, multi-stakeholder approach involving the supplier, the recruitment agencies, and the workers in a transparent manner. We engage immediately in a remediation process, starting with an investigation, leading to the reimbursement of any fees paid. The supplier is also required to implement systemic changes, including a zero-fee policy, to avoid any future recurrence. Throughout the entire process, we provide the supplier’s staff with free access to relevant training resources.
In 2020/2021, six suppliers reimbursed fees to workers totaling US$167,500, while other remediation processes are still in progress.
Capacity building on sustainability
Training our buyers and executives
To increase awareness of responsible purchasing practices, our procurement teams, comprising 285 buyers and procurement managers, attended webinar sessions on supplier and subcontractor due diligence, with a focus on social risk and forced labor and an update on worldwide regulations.
In December, all ST buyers were also enrolled in the RBA’s Responsible Procurement training. By the end of the year, 88 buyers had completed at least one training module. This training will continue in 2022.
In addition, we enrolled our sustainability council members in the RBA Responsible Mineral Sourcing e-learning program to increase their awareness of this important subject.
Training our suppliers
We are not only committed to controlling our suppliers, but also to supporting them in raising their awareness and capability to comply with required standards.
Our aim is to help our suppliers improve their performance sustainably, through dedicated e-learning on risks in areas such as labor (including working hours and forced labor), ethics, health and safety, environment, and management systems.
We deploy supplier e-learning in the RBA training platform, as well as webinars and in-person training. In 2021, we trained over 400 suppliers' employees representing more than 200 companies.
In addition to this, our worldwide community of experts supports suppliers’ continuous improvement through ongoing dialog and sharing best practices. An example of this is the support provided by our ST Muar site (Malaysia) to one of our key suppliers.

Abdul Ghaffar Bin Attan
HR & ESH Manager, MEMC Electronic Materials Sdn. Bhd. (Malaysia)
MEMC Electronic Materials’ Kuala Lumpur team was invited by ST to visit its Muar (Malaysia) site in November 2021. It was a great learning experience to further enhance our knowledge of RBA requirements. The biggest challenge that we have encountered is managing foreign workers. From the visit, we learned that some of ST’s foreign worker management methods could be adopted to improve our practices. The collaboration will be ongoing, with ST sharing information to assist us in enhancing RBA practices.”
Grievance reporting
Like ST employees, our suppliers and their workers are encouraged to use our independent external hotline to share any concerns. This channel is reachable online or by phone in local languages and allows reports to be made anonymously if desired. In grievance cases, ST and the supplier must ensure complainants are protected against any retaliation.
Contributing to the Sustainable Development Goals
Our commitments and programs as described above contribute to:
SDG target 8.7 – Take immediate and effective measures to eradicate forced labor, end modern slavery and human trafficking and secure the prohibition and elimination of the worst forms of child labor.
SDG target 8.8 – Protect labor rights and promote safe and secure working environments for all workers.
SDG target 17.16 – Enhance the global partnership for sustainable development, complemented by multi-stakeholder partnerships that mobilize and share knowledge, expertise, technology and financial resources, to support the achievement of the sustainable development goals in all countries, in particular developing countries.
2025 sustainability goal |
Status |
Comments |
SG20: Conduct an annual risk assessment of our supply chain and audit 100% of our suppliers at risk by 2025. |
Risk assessment conducted |
Annual sustainability goal |
Status |
Comments |
≥ 90% of eligible suppliers signed an agreement to comply with the RBA code of conduct. |
90% |