Waste
Managing our waste
Our waste management strategy is based on the proper classification, separation, and safe disposal of waste. It is driven by local regulations as well as Company policy, with our sites being expected to respect the most stringent of these requirements. Wherever possible, we give priority to reduction, reuse, recycling and recovery over incineration and landfill. Together with our customers and partners, we strive for zero waste, and promote a circular economy. I 103-2 I
Continued performance improvement
In 2021, we reused, recovered, or sent for recycling 90% of the waste generated by our operations. This was two points better than 2020, making good progress towards our 2025 goal of 95%. However, the waste sent to landfill increased to 7% from 6% in 2020, above our annual target of ≤3%. This was caused by an issue with a waste disposal supplier at one of our manufacturing sites. The problem was corrected during the year.
90%
of waste reused, recovered, or sent for recycling
Reducing landfill waste is one of our priorities. Our Shenzhen site (China) successfully passed a third-party certification ‘UL zero waste’ related to landfill waste. It includes an assessment of disposal methods with a focus on reducing the amount of waste sent to landfill as much as possible. Our Calamba site (the Philippines) also joined the initiative.
Waste split in 2021 (%) I 306-2 I
Reducing waste at the source
The best waste is the waste we do not generate. We apply this approach at all our manufacturing sites to minimize unnecessary resource consumption and waste generation across our operations.
In 2021, our Shenzhen (China) site developed a comprehensive strategy to reduce waste at the source in daily operations. The site deployed a waste scorecard to provide a global view of the main waste streams. Based on this analysis, appropriate programs were developed. These include:
- reducing the thickness of the resin used in manufacturing processes, resulting in less resin waste
- compressing cardboard boxes, thereby reducing their volume for storage and transport
- implementing a highly efficient press filter, reducing the quantity of sludge generated by wastewater treatment
- optimizing chemical usage, such as ethanol and flux cleaning in manufacturing processes, reducing chemical consumption and the waste chemicals generated
As a result, the site has reduced the absolute amount of waste generated by 11%.

Haiyan Zeng
Sustainability Manager, Shenzhen (China)
We believe the best way to manage waste is to be waste free. Waste reduction at the source is the priority focus of our innovative waste scorecard initiative. The project, launched in 2021, enables our employees to get involved in exploring various waste reduction opportunities for materials, processes and waste treatment. A series of best practices has been developed to reduce waste sources, including optimizing process parameters, improving cleaning efficiency and optimizing production arrangements. As well as improving our environmental management performance, the project further enhanced the site’s sustainability culture.”
During the year, our Crolles site (France) launched a working group with facilities, environment, health and safety (EHS) and manufacturing teams to reduce sulfuric acid waste. Better waste segregation and the removal of several steps in the process resulted in a decrease of 1,000 tons of waste and 600 tons of raw materials. This also saved 76 tanker journeys between the site and the waste disposal supplier, representing 32,000km and 22 tons of CO2.
Promoting a circular economy
Moving towards a
circular economy
Using waste to create value benefits the environment, people, and our Company. Therefore, we look for opportunities to valorize our residual waste wherever possible.
For several years, we have been implementing various circular economy initiatives to find new uses for the waste generated from our activities.
- Fluoride sludge is transformed into pellets for the metallurgy industry.
- Sulfuric acids are used for recycling batteries.
- Deflashing waste powder is sent for precious metal recovery.
- Palladium is recovered for reuse in the automotive industry.
- Electronic waste is dismantled; some parts are reused, and precious metals are recovered.
- Solvents are sent for distillation and reuse.
- Solvents are burned and the energy recovered.
- Ammonia in wastewater is treated and used in agricultural fertilizers.
- Landfill industrial waste is transformed into solid combustible material and used in cement factory furnaces.
- Silicon wafer scraps are used for aluminum production for the automotive, aviation and photovoltaic industries.
- Paper, cardboard, plastics, and wood are recycled.
- Organic waste is transformed into compost.
- Spent resin and sludge are used in the cement and brick industry.
- COVID-19 protection masks from our French sites are transformed into plastic pellets.
As an example, our Agrate site (Italy) has been working for more than 10 years with a waste recovery company near Milan. Every week, the site sends the company 35 tons of sludge from two wastewater treatment plants for treatment and recycling. The company checks the sludge to ensure there is no trace of heavy metals or hazardous substances. The sludge is locally dried and then sent to cement factories for reuse. Periodically, we audit the waste recovery company to check its processes and procedures meet our high standards. The last audit was at the end of 2021 and no issues were identified.
A new lease of life for
49 tons
of quartz and plastic since 2012
A steady drive towards zero waste has enabled 49 tons of quartz and plastic from scrap photomasks, generated from our Singapore front-end operations, to be reused since the project started in 2012. To ensure the quartz and plastic remain in a reusable state, the team follows a defined process for cleaning and packing. In addition to quartz and plastic reuse, aluminum from the photomask’s pellicle ring is recycled through a local metal recycling company.
FOCUS
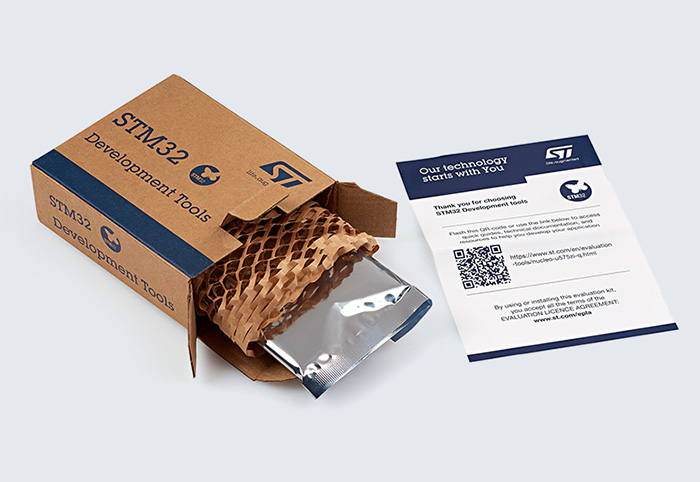
New sustainable packaging
Our STM32 product team is contributing to the collective effort of the Company to reduce its environmental impact. In 2021, it created improved eco-friendly packaging that eliminates the need for plastic blister packs. The new packaging is sustainable for:
- People: the design is better adapted to hardware tools, creating a better user experience. The product also comes with a welcome letter and a QR code that redirects users to the dedicated page on www.st.com, thus eliminating the need for ‘getting started’ user manuals.
- Planet: the box is made from recycled cardboard and uses water-based ink, making it fully eco-friendly and recyclable. The toughness of the box also makes it 100% reusable.
- Business: the design of the box has been optimized for different sizes so that it can be easily adapted to other products. Along with the black and white design, this helps to save a significant amount of resources.
All these changes combined will reduce the annual plastic consumption for STM32 boards by around 15 tons per year.
Controlling hazardous substances
Our various manufacturing processes can generate hazardous or potentially hazardous waste, such as chemical substances and contaminated plastics. We pay attention to all types of hazardous waste (see Chemicals). We seek to identify the best solution among all available treatment technologies to minimize any adverse impact from our activities. In 2021, we identified 41% of our waste as hazardous, 96% of which was reused, recovered, or sent for recycling. The remaining waste was disposed of and treated locally by specially authorized companies.
Contributing to the Sustainable Development Goal
Our commitments and programs related to waste and effluents as described above contribute to:
SDG target 3.9 – Substantially reduce the number of deaths and illnesses from hazardous chemicals and air, water and soil pollution, and contamination.
SDG target 6.3 – Improve water quality by reducing pollution, eliminating dumping and minimizing release of hazardous chemicals and materials, halving the proportion of untreated wastewater and substantially increasing recycling and safe reuse globally.
SDG target 12.4 – Achieve the environmentally sound management of chemicals and all wastes throughout their life cycle, in accordance with agreed international frameworks, and significantly reduce their release to air, water and soil in order to minimize their adverse impacts on human health and the environment.
2025 sustainability goal |
Status |
Comments |
SG16: Reuse or recycle 95% of our waste by 2025. |
90% |
Annual sustainability goal |
Status |
Comments |
SG15: Ensure an annual landfill waste rate below 3%. |
7% |