Waste
We strive for zero waste, by minimizing resource consumption, recycling and implementing circular economy programs.
95%
of waste reused, recovered, recycled
43%
reduction in waste sent to landfill
Zero
waste concept prioritized
Managing our waste
Generating waste is an inevitable part of our operations. Acknowledging this, we have developed a comprehensive waste management strategy to limit our negative impacts. We focus on the classification, separation and safe disposal of waste using an approach driven by local regulations and Company policy. Our priority is to reduce, reuse and recycle and we consider landfill and incineration to be a last resort. I 3-3 I
Improving our performance
95%
of waste reused, recovered, or sent for recycling
In 2022, 95% of the waste generated by our operations was either reused, recovered, or sent for recycling. This achievement allowed us to reach our 2025 target early. We also reduced the quantity of waste sent to landfill from 6.8% in 2021 to 3.7% in 2022. Although this was an improvement, we still fell short of our target of 3%.
Waste split in 2022(1) (%) I 306-3 I
Reducing landfill waste is an ongoing priority. Following the UL zero waste certification of our Shenzhen site (China) in 2021, our Calamba site (the Philippines) successfully passed this third-party certification for landfill diversion in 2022. The UL zero waste validation program focuses on monitoring and measuring material flows through external audits and document validation, with the aim of eliminating landfill disposal. The overall goal was not only waste reduction, but also waste recovery and proper segregation. To facilitate this, the site implemented a number of new initiatives, including ‘no disposable Wednesdays’, color-coded bins, WEEE recycling, and a solid material waste recovery shed (see quote).
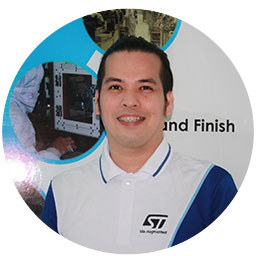
Robert Portento
Environment specialist, ST Calamba (the Philippines)
We started promoting the concept of zero waste in 2021. We implemented a range of waste reduction and recovery programs and encouraged employees to adopt a zero-waste lifestyle, while building management awareness. After promoting these new initiatives, we managed to reuse and recycle 98% of our waste in 2022. At Calamba the journey does not end here, our dedication, passion and collective responsibility towards this cause will continue.”
Striving for less
We believe the best waste is no waste. We apply this approach at all our manufacturing sites to minimize unnecessary resource consumption and waste generation.
Prioritizing
zero
waste
In 2022, our Ang Mo Kio site (Singapore) reviewed its waste management strategy. The process started with waste identification to get a full understanding of the types of waste generated by each department. It also focused on establishing the factors that lead to incorrect waste disposal.
Action points were defined to increase awareness and competency at the site. These included consolidating waste types into a formal library, developing a weblink search feature and developing training to implement the actions identified. Employee outreach initiatives were rolled out to reduce plastic, increase recycling and encourage community mindfulness in relation to reducing our carbon footprint.
Resin is used at our back-end manufacturing sites to encapsulate components. In 2022, our Muar site (Malaysia) implemented a resin recycling system known as co-processing to eliminate disposal of the material to landfill. Co-processing involves using waste materials with energy content as an alternative to fossil fuels. Through this process, the spent resin can be used to heat kilns in the cement industry, reducing waste and, in turn, the carbon footprint of the industry.
The advantages of using cement kilns for waste management include:
- complete burnout of waste due to high temperatures and long resident time
- destruction of the organic component in the waste material due to the high oxygen component of the kiln
- no secondary waste generated during co-processing as the ashes are incorporated into the cement mixture
- no adverse effect on emissions
Through co-processing, our Muar site has reduced the amount of waste sent to landfill from 30% to 2%.
In 2022, our Tours site (France) carried out a study with an external partner to establish a more efficient method for nickel recycling. As a result of the study, it identified a process to extract nickel from a liquid solution using evaporative crystallization. This new process will be implemented in 2023, saving 120 tons of waste annually. The site is also researching a separate system for recycling nickel sludge.
Promoting a circular economy
Moving towards a circular economy benefits the environment, people, and our company. For several years, we have been implementing solutions to create value from the residual waste generated from our activities.
- Fluoride sludge is transformed into pellets for the metallurgy industry.
- Sulfuric acids are used for recycling batteries.
- Deflashing waste powder is sent for precious metal recovery.
- Palladium is recovered for reuse in the automotive industry.
- Electronic waste is dismantled; some parts are reused, and precious metals are recovered.
- Solvents are sent for distillation and reuse.
- Solvents are burned and the energy recovered.
- Ammonia in wastewater is treated and used in agricultural fertilizers.
- Landfill industrial waste is transformed into solid combustible material and used in cement factory furnaces.
- Silicon wafer scraps are used for aluminum production for the automotive, aviation and photovoltaic industries.
- Paper, cardboard, plastics, and wood are recycled.
- Organic waste is transformed into compost.
- Spent resin and sludge are used in the cement and brick industry.
- COVID-19 protection masks from our French sites are transformed into plastic pellets. Since 2021, we have sent more than 5,600kg of masks for recycling.
Managing waste beyond our operations
We launched a regional campaign in 2022 to engage employees in green initiatives and encourage them to reduce, reuse and recycle more. To celebrate Earth Day, a series of events was launched by our sales offices in Seoul (Korea), and Hong Kong, Shanghai and Shenzhen (China). The aim was to propose and develop local initiatives within the framework of ST’s global sustainability strategy. These proposals included quizzes and public awareness programs designed to raise site accountability and contribute to a circular economy.
Focus
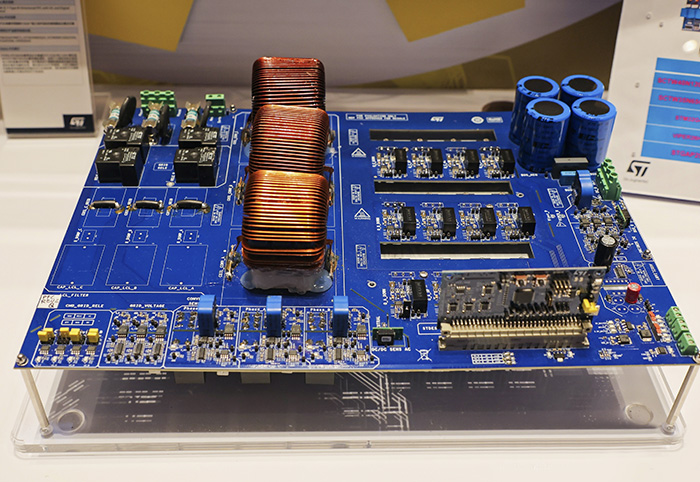
AI to create value from e-waste
Due to changing consumer demands, electronic waste (e-waste) is one of the fastest growing waste streams globally. E-waste includes appliances, such as computers, cell phones or refrigerators, as well as components from manufacturing. Current treatment methods only recover low quantities of precious metals from e-waste, with the remainder being lost and becoming pollutants.
Our Agrate and Catania sites (Italy) collaborated with a research laboratory and waste recycling company to develop a method to monitor and recycle electronic boards more effectively. ST provided electronic boards along with data on components and their material composition to help develop the system.
A machine learning process is applied to the boards to select components through an image processing system. Once the metals are identified, the boards can be appropriately dismantled, and the selected components can be treated together to increase the metal recycling rate. Using AI to optimize the collection, disassembly, and recycling process helps to support sustainable production and consumption, increases resource efficiency, and improves product end of life management.
Controlling hazardous substances
Our various manufacturing processes can generate hazardous or potentially hazardous waste, such as chemical substances and contaminated plastics. We pay attention to all types of hazardous waste (see Chemicals). We seek to identify the best solution among all available treatment technologies to minimize any adverse impact from our activities. In 2022, we identified 42% of our waste as hazardous, 95% of which was reused, recovered, or sent for recycling. The remaining waste was disposed of and treated locally by specially authorized companies.
Contributing to the Sustainable Development Goals
Our commitments and programs related to waste and effluents as described above contribute to:
SDG target 3.9 – Substantially reduce the number of deaths and illnesses from hazardous chemicals and air, water and soil pollution, and contamination.
SDG target 6.3 – Improve water quality by reducing pollution, eliminating dumping and minimizing release of hazardous chemicals and materials, halving the proportion of untreated wastewater and substantially increasing recycling and safe reuse globally.
SDG target 12.4 – Achieve the environmentally sound management of chemicals and all wastes throughout their lifecycle, in accordance with agreed international frameworks, and significantly reduce their release to air, water and soil in order to minimize their adverse impacts on human health and the environment.
2025 sustainability goal |
Status |
Comments |
SG16: Reuse or recycle 95% of our waste by 2025. |
95% |
Annual sustainability goal |
Status |
Comments |
SG15: Ensure an annual landfill waste rate below 3%. |
3.7% |