Waste
We strive for zero waste by minimizing resource consumption, recycling, and implementing circular economy programs.
96%
of waste reused, recovered, recycled
46%
reduction in waste sent to landfill
Zero
waste concept prioritized
Managing our waste
Generating waste is an inevitable part of our operations. Recognizing this, we have developed a comprehensive waste management strategy to limit our negative impacts. We focus on the classification, separation, and safe disposal of waste using an approach driven by local regulations and Company policy. Our priority is to reduce, reuse, and recycle and we consider landfill and incineration to be a last resort. 3-3
Strengthening our performance
96%
of waste reused, recovered, or sent for recycling
In 2023, 96% of the waste generated by our operations was either reused, recovered, or sent for recycling, one percentage point higher than 2022. We also reduced the quantity of waste sent to landfill from 3.7% in 2022 to 1.9% in 2023. This reduction achieved our target of an annual landfill rate below 3%.
Waste split in 2023 (%) 306-3
Zero waste to landfill program
Prioritizing
zero
waste
Reducing landfill waste is an ongoing priority. Following the successful UL Zero Waste to Landfill validation of our Shenzhen site (China) and Calamba site (the Philippines), ST decided to extend the program to all manufacturing sites. The UL Zero Waste to Landfill program is based on the UL2799 standard. It focuses on monitoring and measuring material flows, detailing waste streams to optimize processes, and improving waste management with the aim of reducing waste generation. Recycling and recovery are prioritized to reduce landfill disposal. In 2023, ST waste management teams received training on the UL2799 standard and our sites reviewed their waste management targets. These are the first steps towards implementing the UL Zero Waste to Landfill program across our operations.
Reducing waste generation
We believe the best waste is no waste. We apply this approach at all our manufacturing sites to minimize unnecessary resource consumption and waste generation. Our sites continually analyze processes as an important part of continuous improvement and strive to find innovative methods for waste reduction.
In 2023, several initiatives were implemented to reduce packaging waste. At our Shenzhen site (China), material packing processes were optimized, reducing carton waste by 30 tons and wooden waste by 25 tons. The total waste reduction of 55 tons represented approximately 8% of the total packaging waste generated on site in 2023. These results were achieved through improvements such as implementing interlaced stacking, reducing inner packaging for carton boxes, and standardizing and reducing the size of wooden packings to optimize space.
At our Marcianise site (Italy), single use pallets were replaced with a reusable variety known as Euro pallets. This was achieved by raising awareness of reusable materials across the supply chain and resulted in the reduction of 33 tons of wood waste.
At our Agrate site (Italy), we reduced the volume of ammonia sulfate waste. This was achieved by reducing the quantity of water in the waste composition, increasing its concentration from 5% to 25%. As a result, the volume of waste generated and transported was reduced. This had a positive impact on our transport emissions, which decreased by 50%, while also reducing costs.
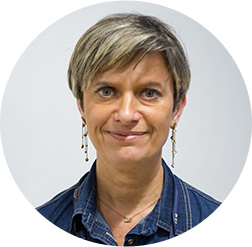
Cinzia Quartini
Water and Ecofacilities Manager, Agrate (Italy)
Our efforts to achieve zero waste and promote a circular economy in Agrate started many years ago. From the pre-selection phase onwards, we choose suppliers and waste disposal methods to maximize the recovery and recycling of waste materials. We are driven by our passion and continually strive for ways to improve waste classification. In 2023, we were able to recycle 98.9% of waste, an achievement I am very proud of.
At our Catania Site (Italy), chemical products used to treat concentrated acid wastewater in the wastewater treatment plant were replaced. As a result, sludge production was reduced by 257 tons, 14% less than in 2022.
Contributing to a circular economy
Thoughtful management of waste can conserve resources and contribute towards a circular economy. For several years, ST has implemented solutions to create value from waste generated by our activities. This is achieved by converting waste into secondary raw materials that can be used in other industries.
- Fluoride sludge is transformed into pellets for the metallurgy industry.
- Sulfuric acids are used for recycling batteries.
- Deflashing waste powder is sent for precious metal recovery.
- Electronic waste is dismantled; some parts are reused and precious metals are recovered.
- Solvents are sent for distillation and reused, or burnt for energy recovery.
- Ammonia in wastewater is treated and reused by other companies as a raw material.
- Silicon wafer scraps are used for aluminum production for the automotive, aviation, and photovoltaic industries.
Our sites actively search for solutions according to the type of waste generated and the local context.
Palladium is recovered from our manufacturing process and deposited on copper cathodes. This is achieved through electrolytic electrodeposition, a process that occurs when an electric current is applied to a solution containing metal ions, causing the movement of the positive ions towards the cathode. Our Agrate site (Italy), has optimized these processes to enable the recovery of 30kg of cathodes with palladium since 2017.
Sulfuric acid waste is diverted at our Crolles site (France) through a partnership with a biofuel producer, reducing the consumption of fossil fuels. Biofuels can be used by trucks, machinery, or generators.
Plastic packaging trays are sent for recycling into resin pellets by our Ang Mo Kio site (Singapore). These can be used to make everyday items, such as crates, clothes fibers, food containers, and bottle caps. The site will divert 5.5 tons of waste from incineration to recycling annually through this initiative.
At our Calamba site (the Philippines), waste including spent resin and sludge is sent to manufacture cement bricks, reducing the use of virgin raw materials. The waste material is used to bind the structure of the cement. Around 29 tons of this waste was diverted in 2023.
FOCUS
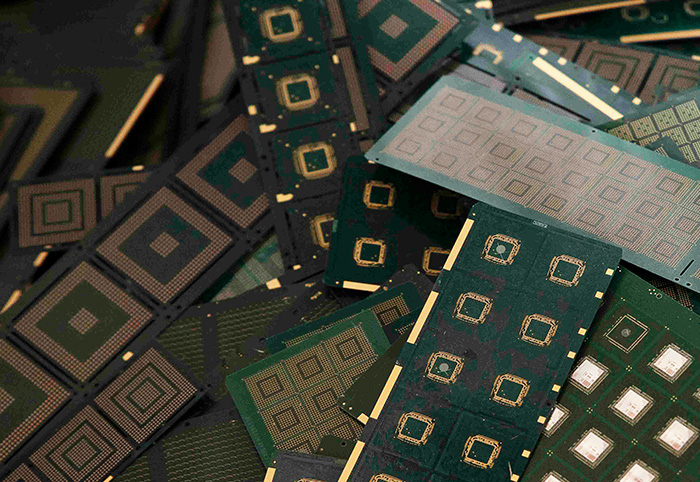
Circularity for precious metals
The use of precious metals can pose several environmental and societal issues. These include human rights concerns related to mining, depletion of natural resources, and associated supply chain uncertainty.
Waste generated at ST’s manufacturing sites can contain strategic metals, such as copper, palladium, silver, and gold. To minimize the risk of negative impacts, we partnered with WEEECycling, an organization dedicated to recovering precious metals and converting them into high quality recycled materials. Waste from our Tours site (France), Bouskoura site (Morocco), and Kirkop site (Malta), was treated using a recovery process consisting of several thermal, chemical, and electrochemical processes. This produces pure secondary materials with the same characteristics as primary/virgin materials. The recycled metals have a significantly lower impact than those from primary extraction and can be reused in the semiconductor, pharmaceutical, and energy industries. This innovative solution results in a very high recovery rate (99%) and a low carbon impact.
The partnership between ST and WEEECycling supports the principles of EECONE, a European project to reduce the impact of the semiconductor industry.
Managing waste beyond our operations
We aim to find innovative solutions for waste management beyond our operations, helping to raise awareness among our employees.
Proper disposal of waste from electrical and electronic equipment (WEEE) is critical for the environment and human health. At our Calamba site (the Philippines), ‘Don’t bin it! Bring it!’ is a program which aims to help ST employees properly dispose of their household WEEE. The program received the good planet prize in ‘Le Trophée Bleu’ sustainability business awards, organized by CCI France Philippines.
At the end of 2023, our Toa Payoh site (Singapore) installed aerobic biodigester food waste composters. The new devices can digest up to 50kg of food waste daily. Due to the use of microbes, nutrient rich fertilizer can be produced for use in-house or in community farms.
Controlling hazardous substances
Our various manufacturing processes can generate hazardous or potentially hazardous waste, such as chemical substances and contaminated plastics. We focus on all types of hazardous waste (see Chemicals). We seek to identify the best solution among all available treatment technologies to minimize any adverse impact from our activities. In 2023, we identified 46% of our waste as hazardous, 96% of which was reused, recovered, or sent for recycling. The remaining waste was disposed of and treated locally by specially authorized companies.
Contributing to the SDGs
Our commitments and programs described above contribute to UN Sustainable Development Goals (SDGs):
SDG target 3.9 – Substantially reduce the number of deaths and illnesses from hazardous chemicals and air, water and soil pollution, and contamination.
SDG target 6.3 – Improve water quality by reducing pollution, eliminating dumping and minimizing release of hazardous chemicals and materials, halving the proportion of untreated wastewater and substantially increasing recycling and safe reuse globally.
SDG target 12.4 – Achieve the environmentally sound management of chemicals and all wastes throughout their lifecycle, in accordance with agreed international frameworks, and significantly reduce their release to air, water and soil in order to minimize their adverse impacts on human health and the environment.
2025 sustainability goal |
Status |
Comments |
SG16: Reuse or recycle 95% of our waste* by 2025. |
96% |
Annual sustainability goal |
Status |
Comments |
||
SG15: Ensure an annual landfill waste* rate below 3%. |
1.9% |
|||
|