Chemicals
It is our priority to responsibly manage chemicals and replace hazardous substances wherever possible.
700+
new risk assessments conducted
100%
DEHP-free across our sites
19,000+
hours of chemical-related training
We carefully manage the chemical substances and materials we use throughout our operations. This allows us to monitor and address our impacts on people and the environment and to comply with legal and customer requirements.
Applying a rigorous approach
Our use and handling of chemicals is led by a precautionary approach, as set out in Principle 15 of the Rio Declaration and in the ST sustainability charter, available at www.st.com/sustainabilitycharter. 2-23
700+
new risk assessments
At each of our manufacturing sites, a chemical committee meets regularly to review and evaluate best management practices for identified hazards. The committee uses a comprehensive approach to make decisions on chemical usage. This includes evaluating chemical compositions, hazards, use conditions, engineering controls, medical recommendations, and industrial hygiene requirements. Risk management measures, personal protective equipment (PPE), waste management, administrative controls, and training requirements are also considered. By rigorously applying this process, we can identify critical substances as soon as they are introduced or reclassified. Modifications to existing processes are also considered and implemented where necessary.
In 2023, we recorded approximately 6,500 chemicals in use across all sites, and conducted more than 700 new risk assessments, achieving nearly 23,000 validated risk assessments by the end of the year.
Since early 2000, we have applied the hierarchy of controls approach to our chemical management procedures. When specific chemicals or materials cannot be eliminated or substituted with less hazardous alternatives, we implement engineering measures and administrative controls to reduce workers’ and environmental exposure. 3-3
Hierarchy of controls
Safety of our people
Our goal is to prevent occupational injury and illnesses for all our workers, and to avoid causing health issues for the surrounding communities. The health of all employees working with chemical substances is monitored through a medical surveillance program. This includes biomonitoring, which assesses an individual’s exposure to natural and synthetic chemicals based on analysis of human tissue and fluid samples.
As an additional precaution, we regularly analyze the air in work areas to verify that our risk management measures are effective. The results are compared to applicable threshold limit values (TLV), which are set by regulatory agencies to ensure safe exposure levels for workers. If the results indicate that the TLV has been exceeded, we take immediate action to identify and address the source of the problem and implement corrective measures to ensure a safe working environment.
In 2023, we conducted over 25,000 measurements, all of which were found to be below 50% of the applicable TLV, which has never been achieved before. This represents a significant improvement, with more measurements taken than any previous year and more than double the measurements taken in 2022. Additionally, less than 5% of the measurements exceeded detection limits (DL), the minimum amount of substance that can be detected, across all tests.
19,000+
hours of training on chemicals
All workers receive specialist training before being assigned potentially hazardous tasks or implementing process changes. This includes instruction and preparation to:
- identify specific hazards
- recognize and understand chemical labels
- apply management methods
- only use equipment in good condition
- select and wear the required PPE
- be ready to react in case of contamination, contact, or an emergency
- ensure preventive maintenance
- properly dispose of spent chemicals according to waste management practices
In 2023, we provided more than 19,000 hours of training on chemical substance management across our manufacturing sites.
FOCUS
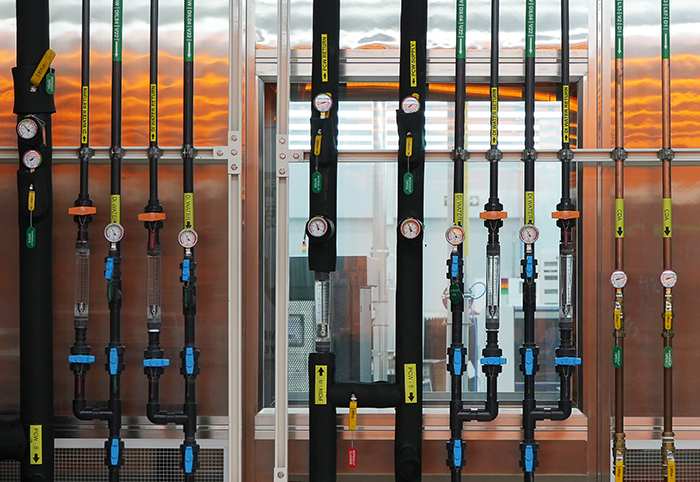
A milestone for our back-end manufacturing
In 2023, our Muar site (Malaysia) introduced a new production line using panel level packaging direct copper interconnect (PLP-DCI) technology. This breakthrough technology offers significant advantages in electrical and thermal performance, while maintaining high standards of performance and quality.
The design and construction phase involved several organizations, including site management, R&D, EHS, and industrial engineering. The teams collaborated to identify and evaluate materials while defining the best technical solutions to implement. During the project definition, there was a focus on employee safety, fire prevention, and emergency preparedness. The environmental impact of the installation was also considered, with evaluation of liquid and air emissions, as well as waste processing.
As a result, a new double piping system was installed to distribute and dispense all necessary chemicals, protecting the workers from any potential exposure. Furthermore, to ensure an adequate level of protection, the chemical storage area, which contains flammable liquid chemicals, was equipped with additional fire protection, a suppression system, and local exhaust ventilation.
The new PLP production line in Muar reflects ST’s priority to support the development of advanced technology while maintaining the highest standards of safety and sustainability.
Protecting the environment
We recognize the importance of reducing environmental emissions, and we have made it a priority to do so in the domains of air, water, and waste. Our approach includes treating emissions where possible (see Water and Waste) and implementing replacement programs for hazardous substances throughout our value chain to minimize our environmental impact.
To further reduce our environmental impact, we have implemented an air emission abatement program that focuses on reducing our emissions of volatile organic compounds (VOCs).
Our air emission abatement program includes the use of advanced technologies and processes to capture and treat air emissions from our manufacturing processes, as well as ongoing online monitoring to ensure that our installations are working effectively.
By reducing our VOC emissions and reducing the use of solvents and other VOC-emitting materials, we are able to minimize our impact on the environment and protect the health and safety of our employees and local communities. Our commitment to reducing environmental emissions in air, water, and waste is an essential part of our overall mission to operate sustainably and responsibly.
Striving for better
Per- and polyfluoroalkyl substances (PFAS) are a large class of synthetic chemicals that possess unique physical and chemical properties. However, they are increasingly recognized as environmental pollutants and have been linked to negative effects on human health and the environment, including flora, fauna, and marine living organisms.
PFAS are used in various stages of the semiconductor manufacturing process, including in equipment and infrastructure. We recognize that our industry needs to reduce its dependence on these chemicals. In close coordination with industry players, we are working to identify and implement non-PFAS technical solutions, looking at the short-, mid- and long-term. This is in line with our longstanding commitment to minimize our environmental footprint at every stage of our products’ lifecycle.
In 2023, we contacted all our direct suppliers and manufacturing subcontractors to assess the presence of PFAS in the products they provide to us or produce for us. We use this evaluation to identify the remaining PFAS in our products to comply with applicable regulatory requirements, such as the US EPA.
Using less
Reducing the use of hazardous substances, including substances of very high concern (SVHC), in our processes and final products helps safeguard the health and safety of our stakeholders, while reducing our environmental footprint. All our manufacturing sites implement specific actions to reduce chemical use.
As an example, our Catania site (Italy) decreased chemical consumption in 2023 to below 2018 levels, despite the introduction of new chemical-intensive processes. This was achieved by reducing the length and complexity of some processes.
Our Shenzhen site (China) initiated a project in 2021 to reduce ethanol consumption, the most used flammable substance. After surveys to understand and analyze the different usages of ethanol, the team defined a reduction plan and improved controls. As a result, the site reduced ethanol consumption by 78% in 2023 compared to 2021 and intends to totally eradicate its use by 2026.
Substituting hazardous substances
We search for the best solutions using technology and innovation to replace hazardous materials in our manufacturing processes. Following the phasing out of chemicals containing perfluorooctanoic acid (PFOA)-related substances in 2022, we finalized the eradication of di(2-ethylhexyl) phthalate (DEHP) in 2023.
Finalizing the DEHP replacement program
In 2012, DEHP used in plastic tapes was added to REACH(1) Annex XIV, preventing its use in Europe. We immediately started a program to replace it, collaborating with our suppliers to identify alternative materials, and with our customers to evaluate and validate potential solutions. As a result, we ensured all products shipped to Europe were DEHP-free by 2013.
100%
DEHP-free
Subsequently, we decided to go beyond the regulations and replace DEHP across all our products worldwide. Due to the complexity of our supply chains, this process took time. In 2021, our sites at Kirkop (Malta) and Shenzhen (China) completed the substitution of DEHP, and in 2023, our Muar site (Malaysia) finalized its replacement.
Replacing DEHP in tapes is the result of a considerable collective effort from on-site teams, suppliers, and customers. It is a milestone that helps us reduce hazardous substances in waste, thereby increasing our ability to recycle the waste we generate.
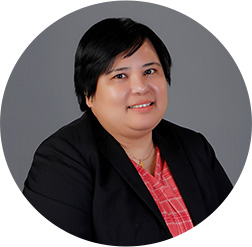
Ramona Marcelino
Material Compliancy – Hazardous Substance Process Management Lead, ST Kirkop (Malta)
As Hazardous Substance Process Management lead, I would like to thank all teams involved in driving the elimination of DEHP in our back-end sites. Their support and teamwork in qualifying DEHP-free material have been exceptional. We have collaborated closely with product groups and customers to expedite material qualification, enabling us to validate solutions quickly and efficiently. It is a great achievement to be DEHP free and contributes significantly to our sustainability goals and reducing the use of hazardous substances.
Aligning with stakeholders’ expectations
Compliance
We adhere to the highest standards to ensure compliance with all applicable regulations on chemicals for our manufacturing sites and our products. It is the responsibility of each site to ensure compliance, based on their specific operations.
When developing new products, their compliance is verified at fixed product development milestones. At the R&D phase, we only consider and select compliant materials to ensure we act in accordance with requirements such as RoHS(2) and ELV(3).
Furthermore, we strive to eliminate the use of restricted substances by design. Thanks to new designs, reduced dimensions, and the lower energy consumption of our chips, we have had ongoing success in decreasing the use of lead in the assembly process (see our ECOPACK results). We also continue to identify new materials with reduced antimony and halogen content.
ST products may be subject to declarations, based on the presence of SVHC. In 2023, we continued to declare new products on the European Chemicals Agency (ECHA) portal to ensure information is available for safe end-of-life disposal.
Across our sites, we continue to work on hazardous substance process management to identify, control, quantify, and report on any hazardous elements in our components, according to the IECQ080000 standard.
Customers
Chemical legislation is evolving globally to reduce environmental impacts during manufacturing. It remains a significant consideration for customers, who closely monitor developments in our products, processes, and compliance.
Information on materials contained in ST products can be found through the IPC 1752 material declaration, which is available at www.st.com. Queries relating to material declaration and substance use accounted for almost 60% of the environment, health and safety (EHS) enquiries we received in 2023.
As a member of the Responsible Business Alliance (RBA), we are working to align with the RBA Industry Focus Process Chemical (IFPC) policy. All chemicals listed in the policy have already been eradicated from our operations. Last year, we completed an IFPC assessment to locate these chemicals within our supply chain. This year, we are working on measures to replace them, prioritizing the recommendations of the Clean Electronics Production Network (CEPN).
Suppliers
We require our suppliers to respect our EHS-regulated substances list, which contains more than 7,700 substances and is regularly reviewed. We also require them to confirm their compliance through analytical certificates, safety data sheets, and commitments. In 2023, 83% of our suppliers committed to our substances’ specification.
Contributing to the SDGs
Our commitments and programs described above contribute to UN Sustainable Development Goals (SDGs):
SDG target 3.9 – Substantially reduce the number of deaths and illnesses from hazardous chemicals and air, water and soil pollution and contamination.
SDG target 6.3 – Improve water quality by reducing pollution, eliminating dumping and minimizing release of hazardous chemicals and materials, halving the proportion of untreated wastewater and substantially increasing recycling and safe reuse globally.
SDG target 12.4 – Achieve the environmentally sound management of chemicals and all wastes throughout their lifecycle, in accordance with agreed international frameworks, and significantly reduce their release to air, water and soil in order to minimize their adverse impacts on human health and the environment.
2025 sustainability goal |
Status |
Comments |
In line with the WSC statement, remove PFOA and PFOA‑related substances in all manufacturing chemicals by 2025. |
Achieved in 2022 |
Annual sustainability goal |
Status |
Comments |
SG19: Follow highest standards for 100% of the materials we use: Hazardous Substances Process Management (IECQ080000) and responsible sourcing initiatives, such as RMI. |
HSPM: 97% |
(1) REACH: Registration, Evaluation, Authorization and Restriction of Chemicals.
(2) RoHS: Restriction of Hazardous Substances.
(3) ELV: End of Life of Vehicles.