Supply Chain Responsibility
Building a responsible supply chain
Supply Chain Responsibility
OUR AMBITION
Systematically assess and mitigate social, environmental, health & safety, and ethical risks in our extended supply chain.
2025 GOAL
100%
suppliers at risk audited
88/500 suppliers audited.
ST is committed to partnering with suppliers who share our values of respecting people and doing business with integrity and excellence. We also require suppliers to apply our standards to their own supply chain.
Our main Supply Chain Responsibility program addresses labor and human rights, safety, ethics and environmental risks in our tier 1 supply chain. It is based on the Responsible Business Alliance (RBA) methodology, adopted in 2006 and deployed progressively since then. It comprises three steps:
As a company with thousands of tier 1 suppliers, it is important for us to identify and prioritize suppliers at risk to include them in our due diligence process. Our annual risk assessment takes into account the type of supplier, the location of their operations (or a specific factory) and the volume of business they do with ST.
In addition to the program for our tier 1 suppliers, we also manage our sub-tier suppliers for raw minerals, see Responsible mineral sourcing section. I 103-1 I 103-2 I
Scalable programs for two categories of suppliers
RBA standard
and methodology deployed in our supply chain
We adapt our level of due diligence to the two different categories of suppliers we manage.
- Direct manufacturing suppliers including manufacturing subcontractors, material suppliers and equipment and spare-parts suppliers. This segment represents the highest percentage of ST’s procurement volume (75%).
- Indirect services including local suppliers such as catering, security, labor agencies or facilities management, which represents 25% of our procurement volume.
Our suppliers I 102-9 I
Procurement volume
2019 OBJECTIVES |
Status |
Comments |
|
≥90% of eligible suppliers signed an agreement to comply with the RBA code of conduct. |
|
93% |
We monitor each category through the three-step process, adapting the level of due diligence by defining the suppliers eligible for each step according to their level of risk.
Direct manufacturing suppliers
- 90% of 200 eligible suppliers have signed a commitment letter and 100% of new direct suppliers have undergone a screening process, including social, environmental and health and safety criteria.
- 85% of 388 eligible supplier facilities have completed an SAQ. 92% are rated low risk and 8% are medium risk.
- 7% of 388 eligible supplier facilities have undergone a third-party RBA VAP audit over the past two years.
90%
of direct manufacturing suppliers have signed a commitment letter
Top five audit findings in our direct manufacturing supply chain(1) I 308-2 I 414-2 I
Indirect services suppliers
- 95% of 252 eligible suppliers have signed a commitment letter and 98% of new indirect suppliers have undergone a screening process, including social, environmental and health and safety criteria.
- 44% of 188 eligible suppliers have completed an SAQ.
- 31% of 188 eligible suppliers have undergone a second-party RBA audit (customer-managed audit) over the past two years.
31%
of eligible indirect services suppliers audited
Top five audit findings in our indirect services supply chain(1) I 308-2 I 414-2 I
We support and monitor our suppliers in implementing the required corrective actions to keep them aligned with our values and standards (see Focus).
177
supplier responsibility audits since 2015
In addition, we regularly evaluate our suppliers’ performance on social, environmental, and health and safety criteria, and we deploy specific programs addressing environmental and safety topics (see Health and Safety; Chemicals; and Waste and Effluents).
In 2019, 76% of our key suppliers were ISO 14001 certified or EMAS validated. I 103-3 I
Helping our suppliers to improve their performance
Our objective is to support our suppliers to improve their performance in a sustainable way, through dedicated elearning on risk issues in areas such as labor (including working hours and forced labor), ethics, health and safety, environment and management systems.
In 2019, we created three dedicated learning paths, comprising both RBA and ST material, all available in the RBA training platform.
- Understanding ST’s approach to sustainability and the RBA standard
- Completing an SAQ
- Preparing for an audit and implementing a corrective action plan
Through this training program, we aim to reinforce the awareness of our suppliers worldwide and to engage them in doing business responsibly.
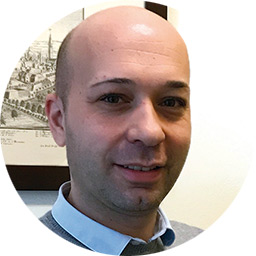
Filippo Rigoli
Project manager, S.A.I.E. spa, construction supplier, Italy
Our collaboration with ST, which began in 1960, has helped us to develop effective management procedures and systems in our construction and maintenance activities, with a particular focus on workers’ rights and on environmental sustainability. The labor and ethics audit undertaken by ST is further confirmation of our shared commitment.”
Quick action to address issues
FOCUS
Remediating forced labor in the supply chain
In 2019, when we discovered an allegation of forced labor related to a labor agent used by a supplier in Malaysia, we took immediate action.
Alerted by an NGO, the RBA informed their members who were customers of the supplier, including ST. ST took the lead in investigating the allegations of unpaid wages, wage deductions to cover work permits and the retention of passports for migrant workers.
When we contacted the supplier, it was unaware of the allegations, as it had paid the labor agent in a timely manner, but after investigating, it confirmed that the labor agent was several months behind with wage payments and had unilaterally made salary deductions.
We, along with the RBA, supported the supplier and assisted it in the remediation process. As a result, the overdue wages were paid (MYR74,000 or US$18,000) to 26 workers and deductions were reimbursed – up to MYR9,000 or US$2,000 per worker. Repatriation was also organized for workers who wished to return home.
This was followed up with a third-party RBA audit and we are assisting the supplier with its corrective action plan. Following this incident, we also reviewed our risk assessment framework and updated the criteria for the type of suppliers at risk.
Responsible mineral sourcing
Our Supply Chain Responsibility approach goes beyond our tier 1 suppliers and covers the responsible sourcing of raw material in our upstream supply chain. In 2019, we had 253 smelters in our tin, tungsten, tantalum and gold (3TGs) supply chain. For the third consecutive year, we successfully validated all of them through the Responsible Minerals Assurance Process. We eliminated four non-compliant smelters from our supply chain and six others ceased operation. We also identified 12 new smelters.
100%
of our 3TGs smelters validated through the Responsible Minerals Assurance Process
As an active participant in the Responsible Minerals Initiative (RMI), we began to monitor our cobalt supply chain during 2019. Multiple reports have highlighted concerns over the social and environmental impacts of cobalt extraction, including child labor and unsafe working conditions in artisanal cobalt mining.
Our first step was to identify the cobalt smelters in the supply chain. The next step will be to use the RMI to ensure we have only validated smelters. In contrast with 3TGs, the lack of existing regulations on cobalt makes the smelter mapping and certification process more challenging. In addition to our own direct influence, we are counting on RMI’s common actions and new regulations to speed up progress in the future.
For more detailed information on our progress, see www.st.com/conflict-free_minerals.
Staying vigilant
Being part of the French business human rights initiative ‘Entreprises pour les Droits de l’Homme’ and RBA helps us better understand and address the risks in our supply chain.
In 2019, we participated in the joint Global Reporting Initiative – Responsible Labor Initiative (GRI–RLI) task force to create a toolkit to encourage reporting on modern slavery across the supply chain. The GRI–RLI task force comprised 14 organizations, including semiconductor, automotive, consumer goods electronics, and retail businesses; and stakeholders, including civil society and socially responsible investors. Working together, we identified common challenges, discussed approaches to addressing them and provided guidance on supportive measures to tackle modern slavery.
Focusing both on our own risks and the external context helps us to comply with due diligence regulations such as the Countering America’s Adversaries Through Sanctions Act, which restricts entry into the US of goods made with North Korean labor, and the ‘Duty of Vigilance’ law in France, for which we received the best due diligence plan prize for 2019 (see Awards).
Contributing to the Sustainable Development Goals
Our commitments and programs related to Supply Chain Responsibility as described above contribute to:
SDG target 8.7 – Take immediate and effective measures to eradicate forced labor, end modern slavery and human trafficking, and secure the prohibition and elimination of the worst forms of child labor.
SDG target 8.8 – Protect labor rights and promote safe and secure working environments for all workers.