Water
Water
OUR AMBITION
Maintain our leadership in water efficiency by reducing consumption, recycling more, and reinforcing our efforts in water scarcity areas.
2025 GOAL
-20%
water consumption*
* Normalized values vs 2016
Over the last 25 years, ST has adopted a comprehensive approach to water management, including water stress assessments, conservation programs, and initiatives with local communities to reduce water extraction and consumption. Through our continuous efforts, we have succeeded in reducing our overall water footprint by 76% (per unit of production). I 103-2 I
Our 2019 performance and actions
Semiconductor manufacturing processes are more and more complex and require an increasing volume of ultra-pure water (UPW) for both front-end and back-end sites.
Against this background, we were pleased to maintain a rate of 41% recycled and reused water in 2019, although our water consumption slightly increased.
76%
reduction in our water footprint over the last 25 years
Conserving water initiatives
Although it is increasingly challenging to reduce water consumption, we continue to implement innovative and creative solutions to minimize the impact of our activity on water availability. We always strive for solutions that optimize the availability of high-quality UPW while minimizing water use.
In 2019, our Calamba site (the Philippines) reduced water consumption by 47,000m3 by replacing the water softener used in the reverse osmosis pretreatment process – the filtration system to produce UPW – with a new anti scalant product. This also reduced our chemical consumption, without affecting the water quality supplied for the manufacturing processes (see Chemicals).
Another reverse osmosis project was successfully implemented at our Agrate site (Italy), substantially reducing water consumption (see Focus).
Meanwhile, our Bouskoura site (Morocco), where water is a scarce resource, developed a new solution to reuse water after the sawing stage of the manufacturing process, saving 100m3 of water per day.
In addition, our Tours site (France) collaborated with a supplier to add sensors to measure water consumption in both facilities and manufacturing areas. The sensors enable us to accurately monitor water consumption and detect any irregularity.
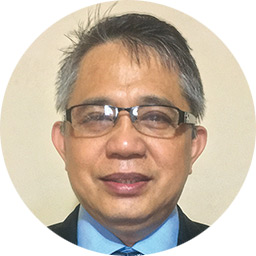
Ignacio Elarco
Facilities Manager – Operations & Maintenance, Calamba (the Philippines)
Our Calamba site (the Philippines) is one of the largest users of chemicals and water in ST, and its consumption has been increasing over the past few years. This presents a tough challenge; however we continue to work to reduce our chemical and water use, with projects such as the reverse osmosis pretreatment process change. I am proud to be able to contribute my 29 years of experience to this kind of project that aims to conserve natural resources and protect future generations.”
Scrutiny from external stakeholders
Once again, we were one of 2,435 companies to participate in the 2019 CDP questionnaire on water security. We achieved a B score, positioning ST higher than the average for the electrical and electronic equipment sector and the global average.
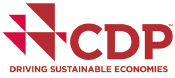
The CDP evaluates our risk assessment practices, water policies, management and performance, as well as our exposure to water-related risks across our value chain. By participating in the CDP, we are able to better understand our risk and increase transparency for stakeholders.
Water preservation and management is an important topic for us and our stakeholders. In 2019, our Shenzhen site (China) was audited by a customer as part of its clean water program. The site was recognized as a best-in-class supplier, joining four of our front-end sites that were audited under the same program in 2015.
A precious resource for all
It is essential to have a reliable water supply for the semiconductor manufacturing process. All ST sites manage their water-related risks according to their needs and water availability. Each site monitors the volume of water it uses and complies with local permits. One of our 11 manufacturing sites uses groundwater for its operations. In 2019, 16% of the total amount of water used at our manufacturing sites came from groundwater and 84% from municipal water supplies.
We firmly believe it is essential to ensure the continuity of water supplies in the areas where we operate. We therefore engage in regular discussions with local stakeholders and implement solutions to reduce water extraction and consumption.
Water withdrawal by source I 303-1 I SDG 6.4
Determination leads to success
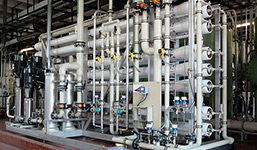
FOCUS
Saving water, saving chemicals and saving energy
Our Agrate site (Italy) initiated a new project in 2019 to use thin-film composite membranes for the reverse osmosis process used to generate ultra-pure water. Although this technology is already widely used elsewhere, previous attempts to implement it at this site had failed due to the chemical make-up of the local groundwater.
The ST team worked for years with industry experts to find the best compromise between membrane brands, field parameters and chemical dosage settings. This determination and collaborative approach eventually delivered a successful outcome, resulting in higher quality ultra-pure water. This in turn led to savings of 30,000m3 of water, 100 tons of chemicals and 540MWh of energy per year.
This technology will now be applied to other systems, enabling us to achieve a more efficient conversion of raw water into ultra-pure water. It will also become the reference case for the water plant at our new manufacturing facility currently under construction.
Typical ST water cycle
Contributing to the Sustainable Development Goals
Our commitments and programs related to Water as described above contribute to:
SDG target 6.4 – Substantially increase water-use efficiency across all sectors and ensure sustainable withdrawals and supply of freshwater to address water scarcity.
SDG target 8.4 – Improve progressively, through 2030, global resource efficiency in consumption and production.
2019 OBJECTIVES |
Status |
Comments |
|
Recycle rate ≥45%. |
|
41% |